- Single Screws & Barrel Sets
- Twin Screw & Barrel Sets
- Segmented Screw Barrel Sets
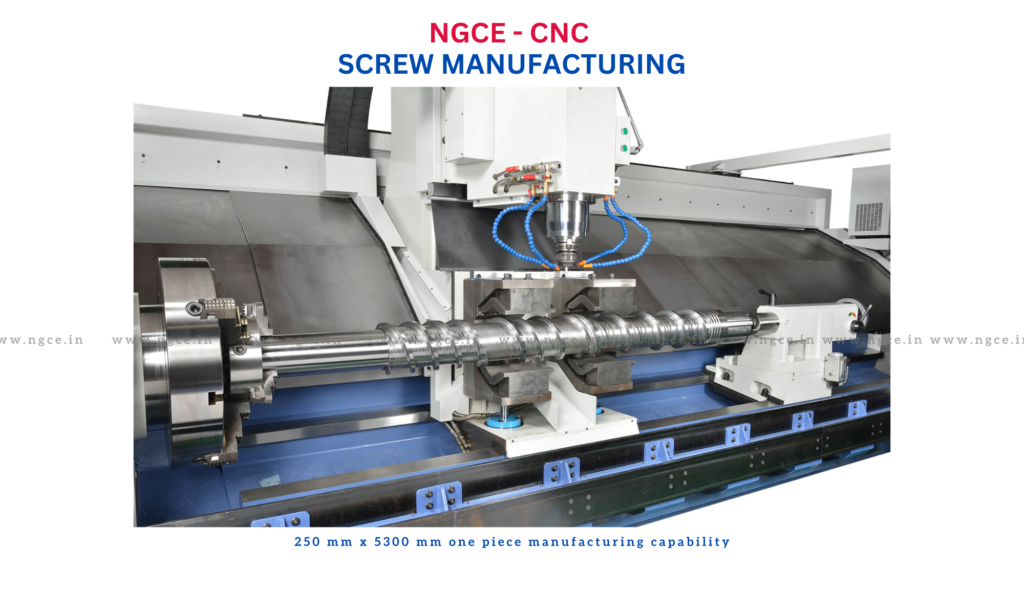
At NGCE, we take pride in being one of the leading feed screw barrel manufacturers in India. We specialize in manufacturing feed screw barrels for polymer processing through plastics extrusion, plastics injection molding, and blow molding. Our products are trusted by some of the largest machine manufacturers around the globe, and we are dedicated to delivering high-quality solutions that meet the specific needs of our customers.
Our team of experts is well-equipped to handle any design, and we have the capability to deal with any steel alloy and bimetallic coating. We understand that the quality of the feed screw barrel is crucial to the efficiency and effectiveness of the processing equipment, and we are committed to delivering superior products that exceed expectations.
At NGCE, we understand that every customer has unique requirements and preferences. That’s why we take the time to listen to our customers, understand their specific needs, and deliver tailored solutions that meet their expectations. We work closely with our customers throughout the entire manufacturing process, from the initial design stage to the final product delivery, ensuring that our products are delivered on time and within budget.
Our commitment to quality, innovation, and customer satisfaction sets us apart from other feed screw barrel manufacturers in the industry. We have a proven track record of delivering high-quality products that meet and exceed our customers’ expectations. Our products are used in a wide range of industries, including automotive, packaging, and construction.
If you’re looking for a reliable and experienced feed screw barrel manufacturer, look no further than NGCE. Contact us today to learn more about our products and services, and how we can help you achieve your processing goals.
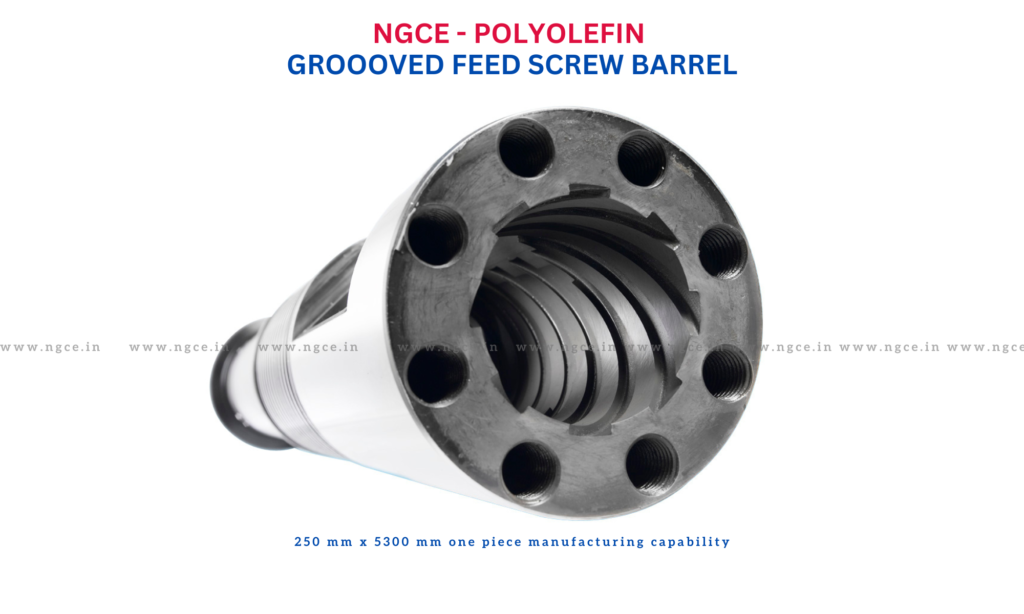
At NGCE, we take pride in being one of the leading manufacturers and designers of grooved feed type barrels for polymer processing in India. We understand that using the right equipment is crucial to achieving the best results, and our grooved feed sleeves are specifically designed to help our customers achieve optimal processing efficiency and quality.
Polyolefins are one of the most commonly used thermoplastics in the industry, and the use of grooved feed type barrels can greatly enhance the processing capabilities and output quality. Grooved feed barrels feature a helical channel that helps in increasing the surface area of the material, which in turn increases the melting efficiency, reduces shear heating, and ensures uniform mixing of the material.
At NGCE, we have a team of experts who have years of experience in designing and manufacturing grooved feed type barrels that are optimized for polyolefin processing. Our grooved feed sleeves are made of high-quality steel alloys and are designed to withstand the most demanding processing conditions. We use the latest technologies and techniques to ensure that our grooved feed sleeves are not only durable but also highly efficient.
We understand that every customer has unique needs, and that’s why we offer customized solutions that are tailored to meet their specific requirements. Our team works closely with our customers to understand their processing needs and provide them with the best possible solutions.
At NGCE, we are committed to delivering high-quality products and services that meet and exceed our customers’ expectations. Our grooved feed sleeves are used by some of the largest machine manufacturers around the globe, and we have a proven track record of delivering superior products that help our customers achieve the best results.
If you’re looking for the best grooved feed barrel manufacturer and designer in India, look no further than NGCE. Contact us today to learn more about our products and services and how we can help you achieve your processing goals.
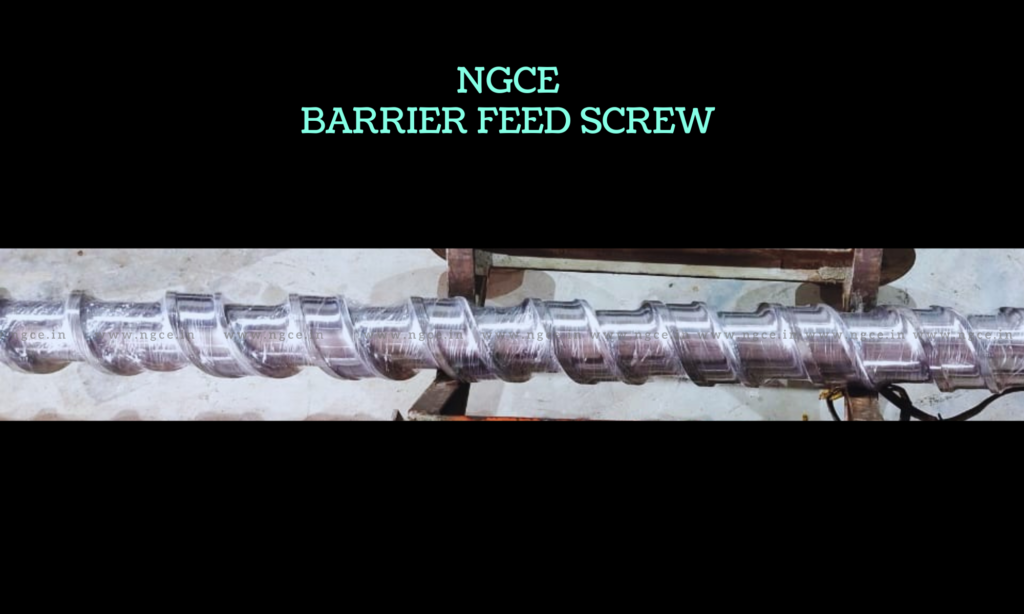
Barrier screws are widely used in the plastic processing industry due to their unique design and numerous benefits they offer. These screws consist of a barrier section that separates the melting and compressing zones, which helps to improve the quality and consistency of the plastic melt. The advantages of barrier screws are as follows:
Improved mixing: The barrier section in the screw creates a pressure barrier that helps to improve mixing of the plastic, resulting in a more homogeneous melt.
Reduced melt temperature: The barrier screw design reduces the shear heating effect, which results in a lower melt temperature. This helps to minimize the possibility of thermal degradation and enhance the quality of the finished product.
Better output quality: Barrier screws provide better output quality, as they reduce the risk of defects such as unmelted particles, air pockets, and black specks.
Increased throughput: Barrier screws have a higher throughput rate due to their ability to process a wider range of materials with varying viscosity and melting temperatures.
There are different types of barrier screws available in the market, including single-flight, double-flight, and barrier/mixing screws. Single-flight screws have a barrier section that extends across the entire screw channel, while double-flight screws have a barrier section that extends across half of the screw channel. The barrier/mixing screw is a combination of the two, featuring a barrier section followed by a mixing section to provide better mixing and melt quality.
In conclusion, barrier screws are an important component in the plastic processing industry due to their numerous benefits, including improved mixing, reduced melt temperature, better output quality, and increased throughput. The type of barrier screw used will depend on the specific requirements of the plastic processing application.
NGCE (www.ngce.in) has extensive manufacturing capabilities for barrier screws in the plastic processing industry. Our team of experienced engineers and technicians utilize the latest technology and equipment to design and produce barrier screws that are tailored to meet the specific needs of our clients. We offer a wide range of options for single-flight, double-flight, and barrier/mixing screws, and we are capable of producing screws with varying lengths, diameters, and pitches. Our quality assurance processes ensure that our barrier screws meet the highest standards of performance and reliability, and we work closely with our clients to ensure that their requirements are met. Whether you need a standard barrier screw or a customized solution, NGCE.in has the expertise and capability to deliver the right solution for your plastic processing needs.

NGCE is a leading manufacturer of vented screw barrels for the plastic processing industry. Our experienced team of engineers and technicians utilizes the latest technology and equipment to design and produce vented screw barrels that meet the highest standards of performance and reliability. We offer a wide range of options for single-flight, double-flight, and barrier/mixing screws, and we can produce vented screws with varying lengths, diameters, and pitches.
Vented screw barrels are used in plastic processing applications where volatiles need to be removed from the plastic melt. They consist of a vent or vents that allow the escape of gas or air during the melting and compression process. The advantages of vented screw barrels are as follows:
1. Improved quality: Vented screw barrels help to remove volatiles and reduce the risk of defects such as voids, bubbles, and surface imperfections, resulting in improved quality of the finished product.
2. Increased throughput: The removal of volatiles from the plastic melt allows for higher throughput rates, resulting in increased productivity and efficiency.
3. Reduced melt temperature: Vented screw barrels reduce the shear heating effect, resulting in a lower melt temperature. This helps to minimize the possibility of thermal degradation and enhance the quality of the finished product.
4. Versatility: Vented screw barrels can be used with a wide range of materials and processes, making them a versatile solution for many plastic processing applications.
At NGCE, we understand the importance of customized solutions for our clients. Our vented screw barrels are designed and manufactured to meet the specific needs of each client, ensuring that they receive the best possible solution for their plastic processing needs. We use only the highest quality materials and our manufacturing processes are subject to rigorous quality control to ensure that our vented screw barrels meet the highest standards of performance and reliability.
In conclusion, vented screw barrels are an important component in the plastic processing industry, offering numerous benefits including improved quality, increased throughput, reduced melt temperature, and versatility. At NGCE, we have the expertise and capability to design and manufacture vented screw barrels that are tailored to meet the specific needs of our clients, ensuring that they receive the best possible solution for their plastic processing needs.
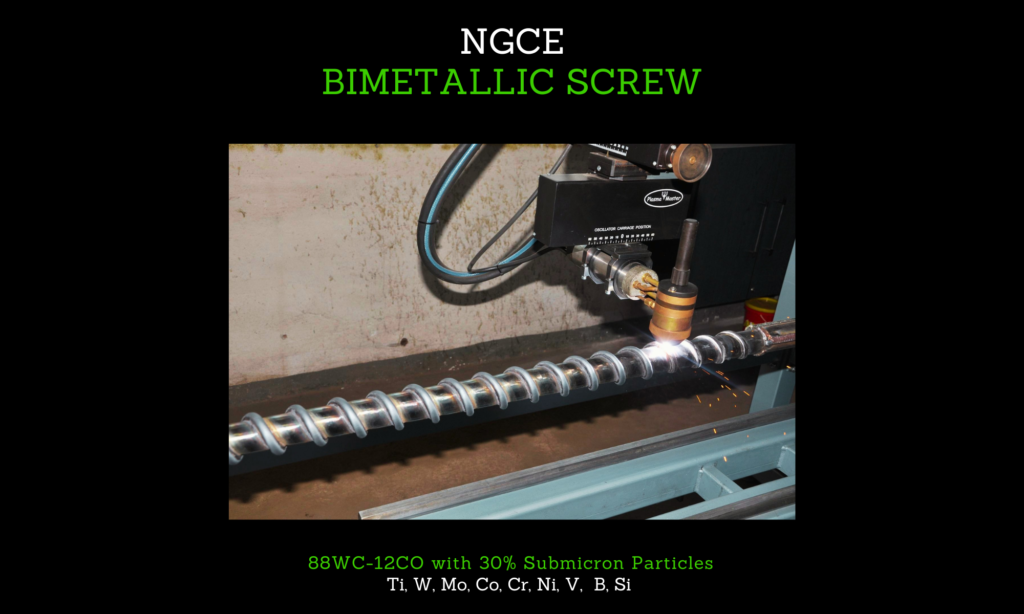
NGCE is a leading manufacturer of bimetallic screws for the plastic processing industry. Our experienced team of engineers and technicians utilizes the latest technology and equipment to design and produce bimetallic screws that meet the highest standards of performance and reliability. We offer a wide range of options for single-flight, double-flight, and barrier/mixing screws, and we can produce bimetallic screws with varying lengths, diameters, and pitches.
Bimetallic screws are used in plastic processing applications where high wear resistance and durability are required. They consist of two materials, typically a high-wear resistant material on the surface and a lower-cost material as the core. The advantages of bimetallic screws are as follows:
1. Increased wear resistance: Bimetallic screws provide increased wear resistance compared to conventional screws, resulting in longer service life and reduced downtime.
2. Improved process stability: The use of bimetallic screws results in improved process stability due to the consistent performance of the screw, resulting in improved product quality.
3. Customizable solutions: Bimetallic screws can be customized to meet the specific needs of each client, ensuring that they receive the best possible solution for their plastic processing needs.
At NGCE, we offer customized bimetallic screws with our proprietary Superalloys formulas that include a combination of Titanium, Tungsten, Molybdenum, Cobalt, Boron, Silicon, Vanadium, and Nickel. Our Cermet range includes Boride, Carbides including pure WC (tungsten-carbide). We are the only company that offers customized coating with a customized formula to suit the budget and process requirements of each client. Our materials are subject to rigorous quality control to ensure that our bimetallic screws meet the highest standards of performance and reliability.
In conclusion, bimetallic screws are an essential component in the plastic processing industry, providing increased wear resistance, improved process stability, and customizable solutions. At NGCE, we have the expertise and capability to design and manufacture bimetallic screws that are tailored to meet the specific needs of our clients, utilizing our proprietary Superalloys formulas and Cermet range. We are committed to providing our clients with the best possible solution for their plastic processing needs, ensuring maximum performance and durability at a competitive price.
All content on this website, including text, images, graphics, and logos, is the property of NGCE and is protected by international copyright laws. Unauthorized use or reproduction of any content on this website is strictly prohibited and may result in severe civil and criminal penalties. Copyright infringement is a serious offense, and NGCE will pursue all legal remedies available to protect its intellectual property rights.